What is Stainless Steel?
Home Stainless What is Stainless Steel?
Stainless steel is a corrosion-resistant alloy of iron, chromium and, in some cases, nickel and other metals.
Completely and infinitely recyclable, stainless steel is the “green material” par excellence. In fact, within the construction sector, its actual recovery rate is close to 100%. Stainless steel is also environmentally neutral and inert, and its longevity ensures it meets the needs of sustainable construction. Furthermore, it does not leach compounds that could modify its composition when in contact with elements like water.
In addition to these environmental benefits, stainless steel is also aesthetically appealing, extremely hygienic, easy to maintain, highly durable and offers a wide variety of aspects. As a result, stainless steel can be found in many everyday objects. It also plays a prominent role in an array of industries, including energy, transportation, building, research, medicine, food and logistics.
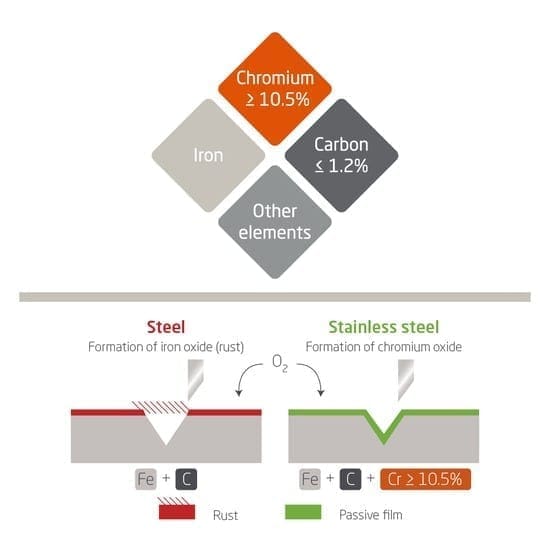
Composition of Stainless Steel
Steel is an alloy of iron and carbon. Stainless steels are steels containing at least 10.5% chromium, less than 1.2% carbon and other alloying elements. Stainless steel’s corrosion resistance and mechanical properties can be further enhanced by adding other elements, such as nickel, molybdenum, titanium, niobium, manganese, etc.
Reaction to Contact with Air, Humidity or Water
On contact with oxygen, a chromium oxide layer is formed on the surface of the material. This passive layer protects it and has the unique ability to repair itself.
General Properties of Stainless Steel
Aesthetics
Stainless steel has a great variety of surface finishes, from matt to bright and including brushed and engraved. It can be embossed or tinted, making stainless a unique and aesthetic material. It is often used by architects for building envelopes, interior design and street furniture.
Mechanical Properties
Compared to other materials, stainless steel has strong mechanical properties at ambient temperatures – it is steel after all! In particular, it combines ductility, elasticity and hardness, enabling it to be used in difficult metal forming modes (deep stamping, flat bending, extrusion, etc.) while offering resistance to heavy wear (friction, abrasion, impact, elasticity, etc.). Furthermore, it offers good mechanical behaviour at both low and high temperatures.
Resistance to Fire
Stainless steel has the best fire resistance of all metallic materials when used in structural applications, having a critical temperature above 800°C. Stainless steel is ranked A2s1d0 for fire resistance with no toxic fume emissivity.
Corrosion Resistance
With a minimum chromium content of 10.5%, stainless steel is continuously protected by a passive layer of chromium oxide that forms naturally on the surface through the reaction of the chromium with oxygen from air or water. If the surface is scratched, it regenerates itself. This particularity give stainless steels their corrosion resistance.
Cleanability
Stainless steel items are easy to clean, usual cleaning products (detergents, soap powders) are sufficient and do not damage the surface. Stainless steel fully meets the requirements of decoration and cooking utensils that require frequent and effective washing.
Recycling
Stainless steel is the “green material” par excellence and is infinitely recyclable. Within the construction sector, its actual recovery rate is close to 100%. It is environmentally neutral and inert when in contact with elements such as water and it does not leach compounds that might modify their composition. These qualities make stainless steel ideally suited to building applications exposed to adverse weather, such as roofs, facades, rainwater recovery systems and domestic water pipes. Stainless steel’s longevity fulfils the requirements of sustainable construction, and effective erection, installation and low maintenance guarantee the user an unrivalled service life.
Stainless Steel Families
With five categories of stainless steels available – each differentiated by the alloying elements added to iron, carbon and chromium – we offer a complete range of solutions.
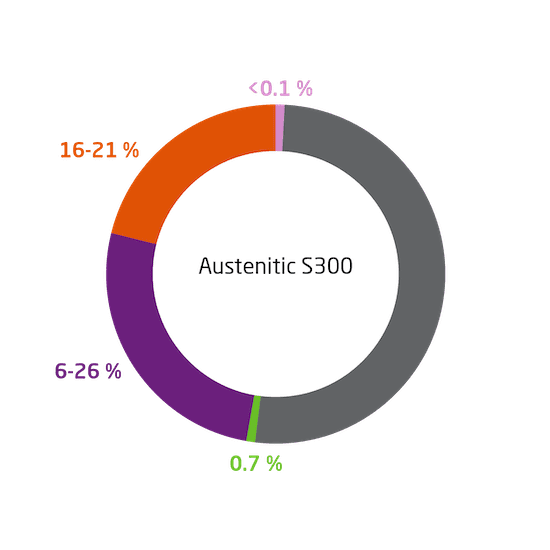
- Austenitics or 300 series
0.015 to 0.10% carbon, 16 to 21% chromium, 6 to 26% nickel, 0 to 7% molybdenum. The presence of nickel improves corrosion resistance in certain media and makes stainless steel more ductile. The presence of molybdenum further enhances the resistance to corrosion in an acid medium. The most common grades are 304/304L and 316/316L. - Applications
Boiler market, aeronautics, electronic components, railway equipment, tubes, chemical tanks and food vats, marine applications, containers, etc. - Heat resistant steel applications
Heating systems, resistor jackets, furnace equipment.
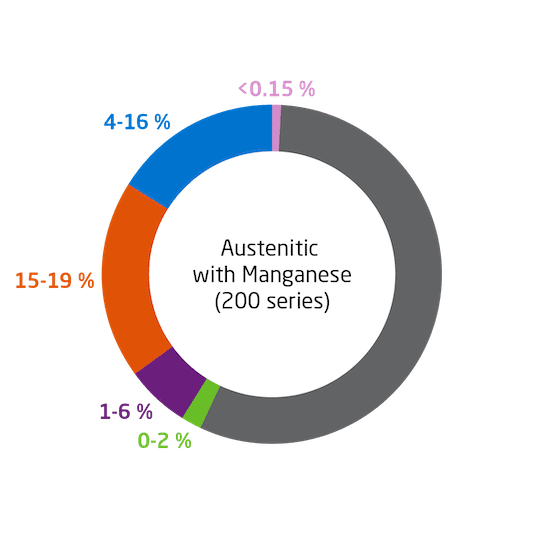
- Austenitics with manganese or 200 series
These are chromium manganese steels, with a low nickel content (always below 5%). - Applications
Asphalt tankers, tubes, food containers, silos, conveyor chains, safety soles, etc.

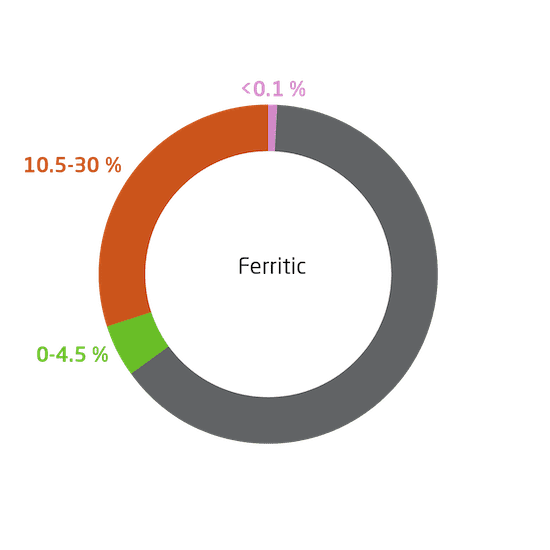
- Ferritics or 400 series: the KARA ferritic offer
0.02 to 0.06% carbon, 10.5 to 30% chromium, 0 to 4% molybdenum. Commonly used internally, these grades are now being developed for envelope and structural products. - KARA is the Aperam brand for ferritic stainless steels
Unlike other stainless steels, the KARA range doesn’t contain nickel and is thus immune from the erratic price fluctuations of this alloying element. As a result, prices are more stable over time, giving KARA a strong argument in the construction sector where project cost and economic design are key elements. - Applications
Car exhaust systems, conveyor chains, cooking utensils, boilers, domestic appliances, trim, dishware, heating, hot water tanks, tubes, etc.

- Austeno-ferritics or Duplex
0.02% carbon, 0 to 4% molybdenum, 1 to 7% nickel and 21 to 26% chromium. These stainless steels not only offer excellent quality, because of their low nickel content – a material that suffers from highly speculative prices – they are also very cost effective. - Applications
Oil, gas, pulp and paper, desalination sectors, chemical industry, etc.
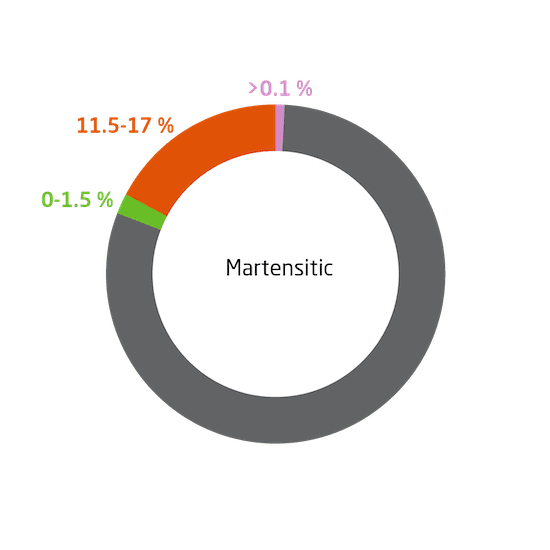
- Martensitics
0.1% carbon, 10.5 to 17% chromium. - Applications
Cutlery, cutting tools, hand tools, springs, etc.