CO2 & Energy
Home Sustainability Environment CO2 & Energy
Environmental Sustainability
As a sector with a high level of CO2 emissions, steel companies like Aperam must take specific steps to reduce their carbon footprint and achieve energy savings: it’s part of our responsibility and a duty towards future generations.
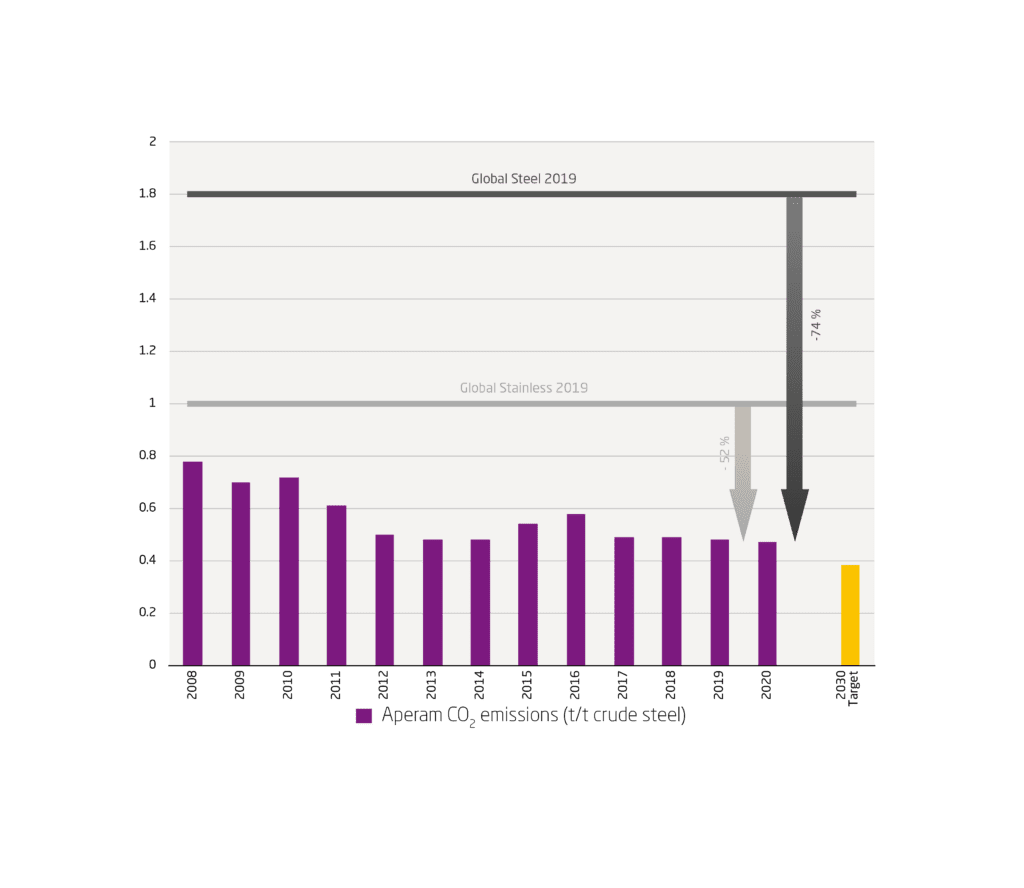
Aperam’s CO2 performance and strategy
Aperam continues to have an industry-leading carbon footprint (scope 1+2)*, which is regularly confirmed by comparisons versus peers using externally-verified figures. This is the result of three key factors:
- Our European electric arc furnaces use as much scrap metal as possible instead of extractive raw materials when economically viable. Aperam is already using over 88% of scrap in its European EAFs, on average, and is working on further increasing its scrap intake.
- On top of having a very low level of energy consumption, we also use a low-carbon energy mix in our melting shops.
- We are operating more than 100,000 ha of FSC®-certified forest in Brazil to produce our own charcoal, which we then use in our steel-making process as a natural and renewable substitute for fossil fuels (coal-based coke).
As to this last point, Aperam can also be considered an agriculture company as we maintain eucalyptus forests and carbonize the trees to sustainably produce our own charcoal and entirely eradicate the use of extractive coke. You can read more about our BioEnergia forest here.
* A total CO2 footprint aggregates a company’s emissions (scopes 1+2) with those emitted upstream of the process (called “scope 3a”, it covers all production input, from raw materials to travel and computers) and the downstream footprint (“scope 3b”).
Refining an Already Best-in-Class CO2 Performance
In its drive to continuously improve its environmental performance, Aperam recently announced several objectives to enhance our environmental excellence. These include the goals of further reducing our carbon emissions (-20% scope 1+2+3 vs 2021) by 2030 and contributing to global carbon neutrality in 2050, objectives that apply to all our steel-making units. You can find more information about our 2030/2050 objectives here. Since 2017, our CO2 footprint intensity has been consistently well below the industry average of 0.83 tCO2e/tcs (World Stainless, scope 1+2). Today, our (scope 1+2) footprint, taking into account the carbon sequestration of our FSC-forest, is amongst the best-in-class, at 0.34 tCO2e/tcs – meaning Aperam has nearly achieved its former CO2e 2030 objective of -30% vs. 2015. In terms of scope 3 emissions, in 2024 we reported a global scope 3a of 2.12 tCO2e/ton, of which scope 3.1 is 1.85 tCO2e. Our scope 3b is much less at 170 kgCO2 e/ton, while our global scope 3 intensity is 2.20tCO2e/ton. Without its own forest’s sequestration, driven by sustainable forestry management and externally certified, Aperam’s global footprint (scope 1+2+3a) is 2.66 tCO2e/tcs. With sequestration, it stands at 2.45 tCO2e/tcs.
Energy Mix and Performance
Aperam’s energy mix remains a subject of pride, with 39% coming from renewable charcoal biomass. In fact, renewables now account for 52% of our total energy use which, in 2023 was 13.8 GJ/tcs or 3.8 MWh/tcs2. As for electricity, in 2023, our global carbon footprint decreased in our main countries of operation. In addition to lowering the emission factor of our electricity suppliers, several other actions have had a positive effect, meaning we remain on track to achieve our target of an 11% reduction in energy use by 2030.
But even with this success, we refuse to stand still and thus remain committed to pursuing other renewable energy sources, including wind and solar power. In fact, our production plants in Genk, Châtelet and Isbergues have all recently installed windmills and/or solar panels. The solar installation at our plant in Genk produces nearly 20 GWh of power every year, covering almost 5% of the site’s electricity needs. Likewise, the 15,000 panels installed at our Châtelet plant have an installed capacity of 6.0 MWp and an expected annual production of 6,300 MWh of green electricity.
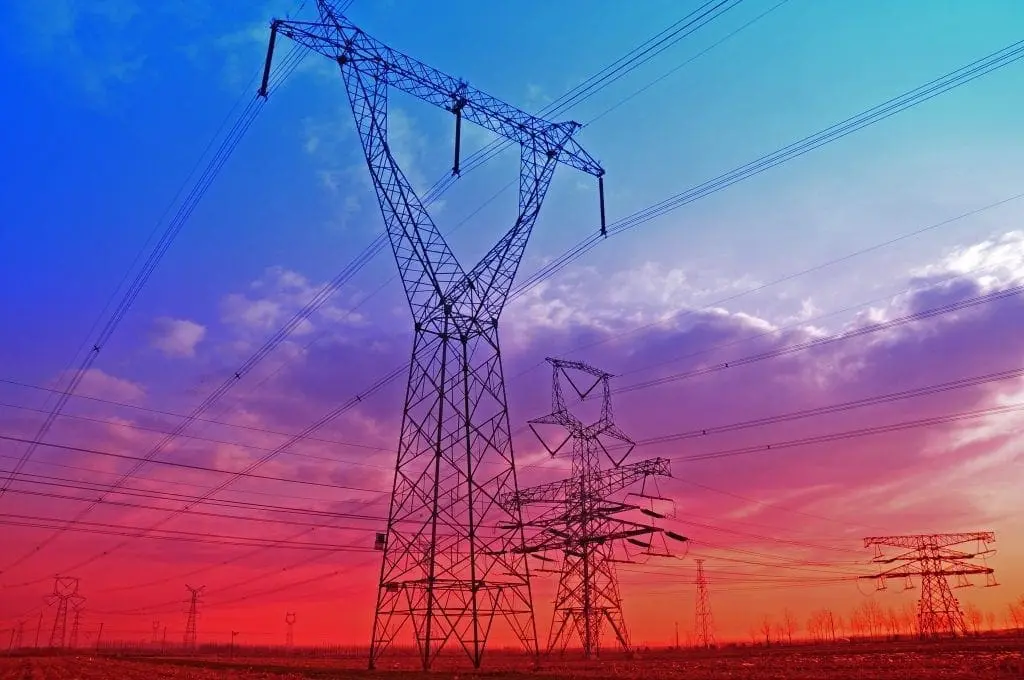